Continuous Flow Reactors
What are Continuous Flow Reactors?
A continuous flow reactor is the reactor vessel used in flow chemistry applications. Flow Chemistry is a synthetic technique which is complementary to traditional batch methods. Fundamentally Flow Chemistry is a tool for increasing the control of the key reaction parameters chemists use to selectively control their reaction pathways.
To understand what a flow reactor can offer we need to understand the difference between batch and flow techniques.
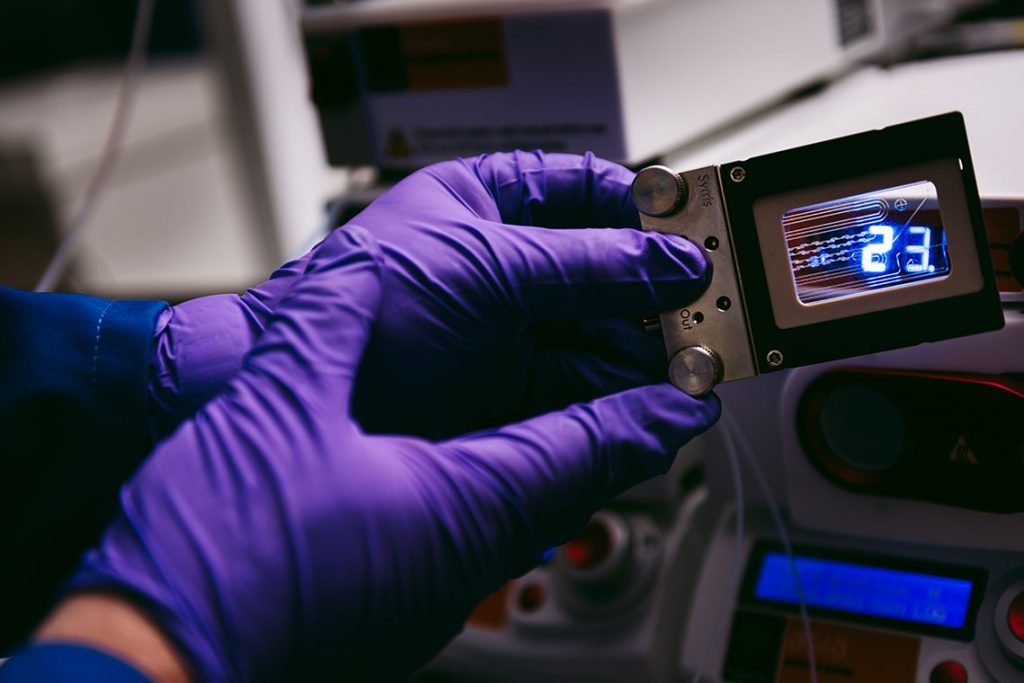
Batch vs Continuous Flow Chemistry
Batch Flow
Batch chemistry is the traditional way to perform chemistry that everyone will be familiar with. Our reagents are loaded into the reactor, mixed, and left to react. We may look to heat or cool the reactor or activate our chemistry by electrochemical or photochemical means. When the reaction is complete the products is collected, worked-up and the product isolated.
Continuous Flow
Continuous flow chemistry is a different way to perform a chemical reaction. Flow chemistry is the process of performing chemical reactions in a continuous tube or capillary. Our reagents are pumped together at a mixing junction and the flow continues down a the tube which can also be heated or cooled or irradiated with photons (photochemistry) or have a potential applied across it (electrochemistry). We still perform the same chemistry but the desired product is continuously eluted from the continuous flow reactor. The product still needs to be collected, worked-up and isolated.
Types of Continuous Flow Reactors
There are many configurations of continuous flow reactors that are employed in flow chemistry systems. The most common types of flow reactor fall into one of three categories.
Chip-based Reactors
These reactor types range from small glass teched microreactors to larger “plate” based reactors of silicon carbide for manufacturing. They offer the best heat transfer characteristics from their extremely high surface area to volume ratios. Their manufacture offers advantages in the wide range of geometries that can be etched including complex mixing sections.
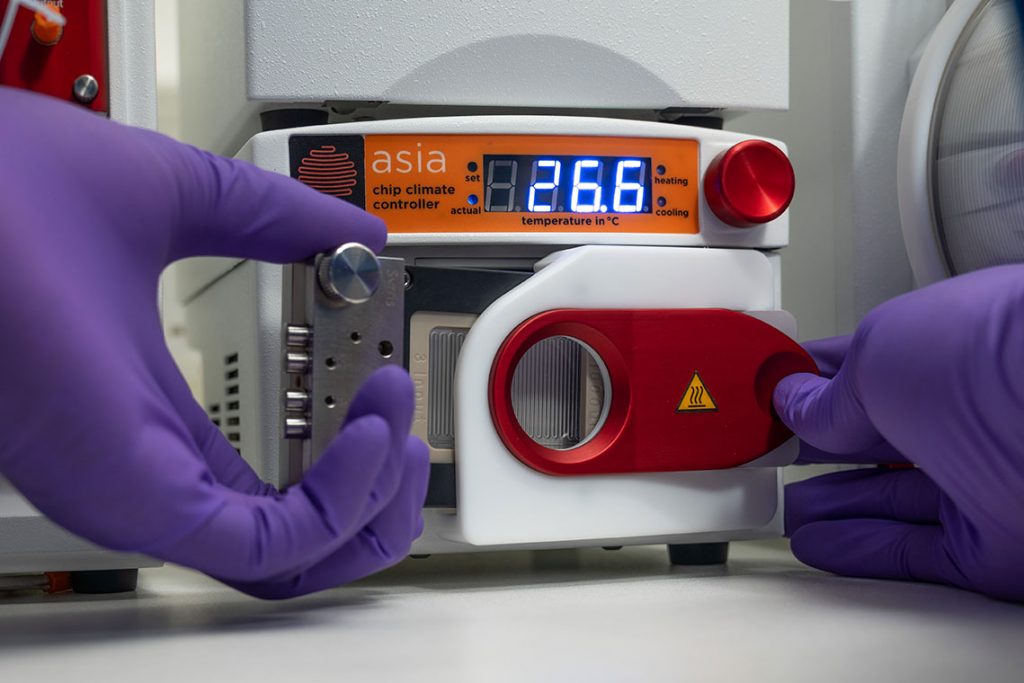
Coil-based Reactors
These reactors are typically made from a length of tubing that can be heated or cooled via a dedicated thermostat unit. Their construction is generally PFTE, PFA or Stainless Steel depending on the temperatures and pressure required and the associated chemical compatibility of the reaction. These are the most used continuous flow reactors due to their lower cost compared to chip-based reactors.
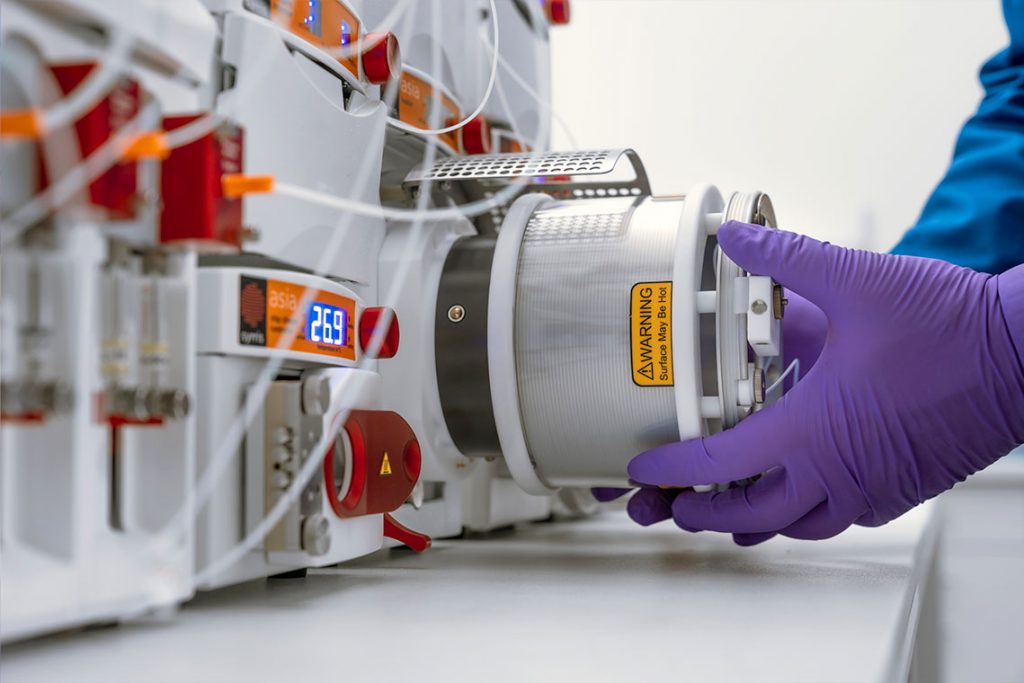
Packed Bed Reactors
If heterogeneous catalysts or reagents are required then packed bed reactors, or solid-phase reactors, are generally used. These are commonly made up of a column or cartridge constructed of glass or stainless steel. The solid reagent is packed into these and the reaction solution is passed through the column. There are several advantages of these reactors, the molarity of the reagent is much higher, and it removes the need for separation on completion of the reaction.
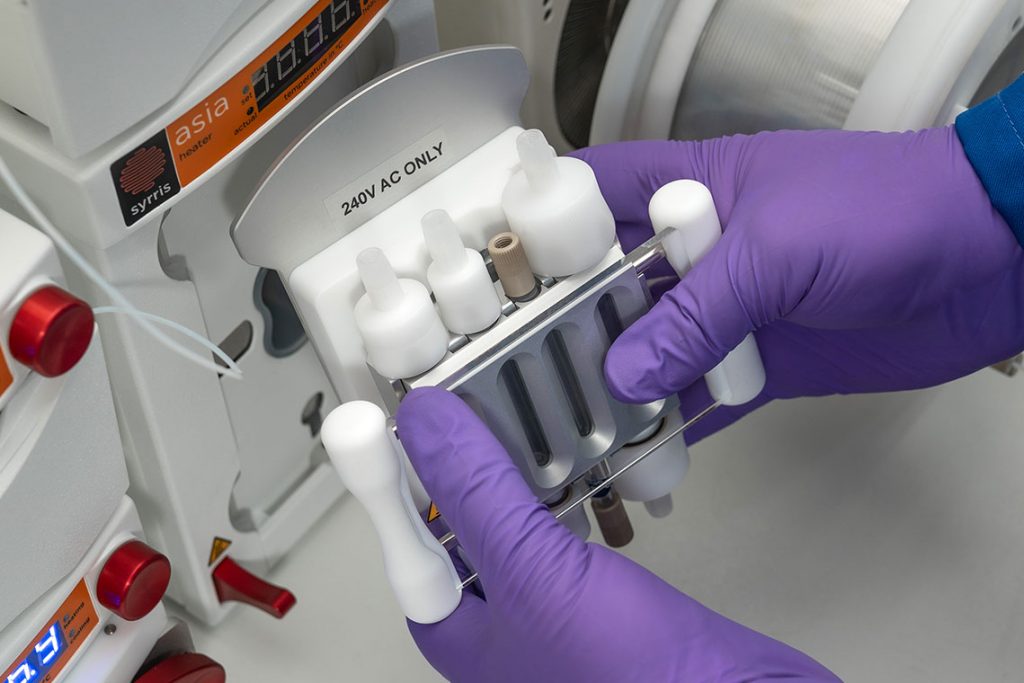
Flow Chemistry Fundamentals
Flow chemistry is all about controlling our reaction conditions. If we can do this with precision, we can harness the benefits and advantages that this synthetic technique can offer.
Whether we perform our chemistry in a batch or flow reactor we need to consider many parameters such as reaction time, reaction temperature, mixing and addition rates and molar ratios of reactants.
When we perform a flow experiment practically, we still need to consider the same reaction parameters and conditions. In a continuous flow reactor precise control of the following is made easier.
- Control addition and mixing
- Control stoichiometric equivalents
- Control reaction times
- Control reaction temperatures
If we consider the schematic of a flow chemistry reaction as shown below we can illustrate how this is achieved.
We start with solutions A and B of our reactants of a known concentration. These are introduced into the fluidic pathway either directly through the pump (from a bottle) or via a reagent injector (if we’re introducing smaller amounts). These are pumped into our flow system and are bought together and mixed. They then travel through our continuous flow reactor and are collected.
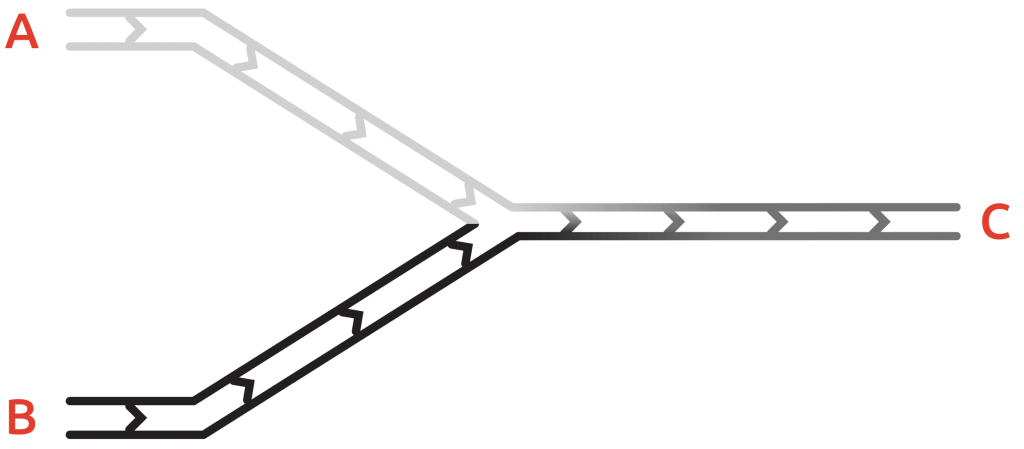
- We can control the flow rate of the pump that introduces both reagent solution therefore we can control the rate of addition and the rate of the reactants relative to each other. By knowing this we can precisely control the stoichiometry (molar ratio of reactants) of our reaction.
- We know the flow reactor volume so we can also control the length of time our reactants spend in the reactor environment.
- The flow reactor has a large surface area to volume ration so it’s easier to control reaction temperature through the increased heat transfer characteristics.
Benefits of Flow Chemistry
The precise control of reaction parameters that flow chemistry offers give us many benefits over traditional batch techniques. A quick review of published papers citing flow chemistry will often show a combination of these benefits making this an important addition to the chemists tool box.
Faster reactions |
Allows us to potentially increase reaction rates via pressurization and increased mixing characteristics. |
Safer reactions |
Allows us to potentially reduce associated hazards via a smaller inventory of material reacting at any time and increased control of exothermic reactions. |
Faster reaction optimisation |
It enables a fully automated, walk-away process to explore both continuous parameters such as time, temperature, molar ratios and discontinuous variables for reagent screening. |
Reaction conditions not possible in batch |
Allows us to form reactive intermediates and hazardous reagents in-situ amongst other examples. |
Fast serial library synthesis |
Automation allows the easy exploration of diverse chemical space via automated liquid handlers. |
Reactions are usually more selective |
Through the increased control of reaction parameters. |
Scale up is easier in flow than batch |
Direct scale up from mg’s – kg’s with minimal re-optimization required. |
Simple reaction work-up in flow |
Methods such as liquid-liquid extraction reduce the number of handling steps. |
Easy integration of in-line reaction analysis |
Real-time feedback on reaction progression. |
Features of a Continuous Flow System
There are certain key elements that are required to build any flow chemistry system. The basic requirements for any flow chemistry system are, however, quite simple. We need a pump to introduce our reactants, a continuous flow reactor to perform our chemistry and maybe a back pressure regulator to allow us to heat above reflux temperatures.
Modern flow chemistry systems such as Syrris Asia Flow Chemistry System come with lots of benefits over simple flow set-ups. Flow chemistry is a modular technique so a system that offers a complete range of components is favorable. These can be broken down into the following subsets of functions.
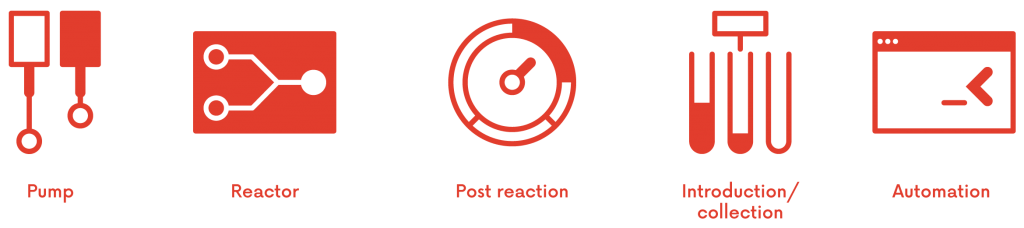
Pump |
The pump is the most important part a flow chemistry system, it can be described as the “heart”. Without confidence in flow rate accuracy and precision most of the benefits of flow chemistry are lost.
A pump needs a wide flow rate range, minimal pulsation and high chemical compatibility to pump the widest range of chemicals. |
Reactor |
The continuous flow reactor is the second most important part. A flow system requires a reactor that has excellent chemical compatibility and is able to cover a wide rang of reaction temperatures. Often chemists will want to explore a range of residence times and chemistries so a range of reactor volumes and types should be considered.
With the added benefits of using novel reaction activation methods such as photochemistry and electrochemistry flow reactors that can exploit these techniques are desirable. |
Post Reaction |
Post reaction modules describe functions after the flow reactor. A back pressure regulator is essential to work above reflux temperatures and use reactive gases. Phase separation modules can be added for continuous liquid-liquid extraction and quenching to enable in-line work-up. We can also add modules to sample, dilute and add aliquots of our reaction to off-line analytical detectors such as HPLC. |
Introduction and Collection |
The simplest methods to add reagents is via the pump, however, we can use reagent injectors to introduce smaller amounts that make reaction optimization more efficient. The use of automated reagent injectors allows us to explore reagent screening and library generation.
Automating reaction collection with liquid handlers allows us to collect a series of reactions hands-free. |
Automation |
Having a control software that can precisely control reaction conditions and the complete range of functions available in a flow chemistry system allows for more efficient “walk-away” processes. The software should be easy to use with “chemist familiar” terms (reaction time, temperature, concentration, etc.) and able to calculate timings and flow rates etc.
Having open control of the range of modules also allows for the programming and integration of a range of analytical detectors for applications such as machine learning, closed-loop optimization. |
Main Applications for Flow Chemistry
Continuous flow chemistry has been applied to an ever-expanding number of fields in the last 20 years. The increase in the flow chemistry publications illustrate how chemists are exploiting this enabling synthetic technique for a varied range of applications.
Once the domain of academic groups and the Pharmaceutical industry flow chemistry is now finding applications in a diverse range of industry. CRO’s are using the technique pioneered by larger research companies. Material chemists are using flow chemistry for the formation of nanoparticles and polymers. The flavour and fragrance industries where volatile compounds are common are seeing benefits. The oil and paint industries are using flow to create additives. The breadth of industries using flow chemistry is too long to list.
Flow Chemistry Equipment
The Syrris Asia Flow Chemistry System is a range of award winning flow chemistry modules that enable the widest variety of flow chemistry applications.
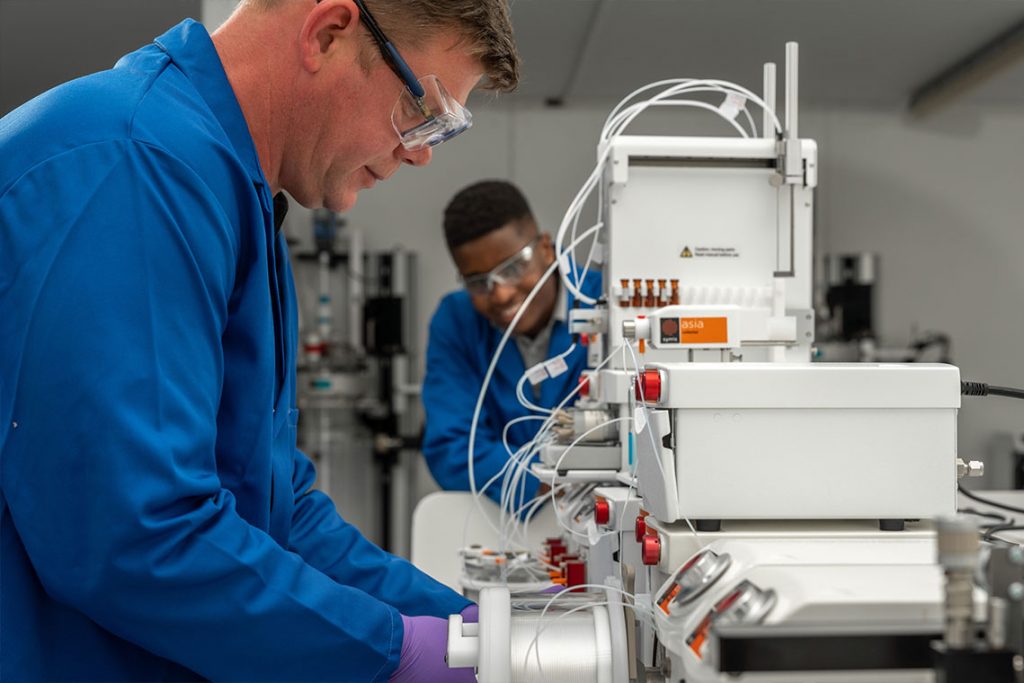
Contact our team of specialists to find out how the Syrris Asia Flow Chemistry System could help your chemistry applications.